Is Your Air Clean?
Published date: 28 Apr 2022
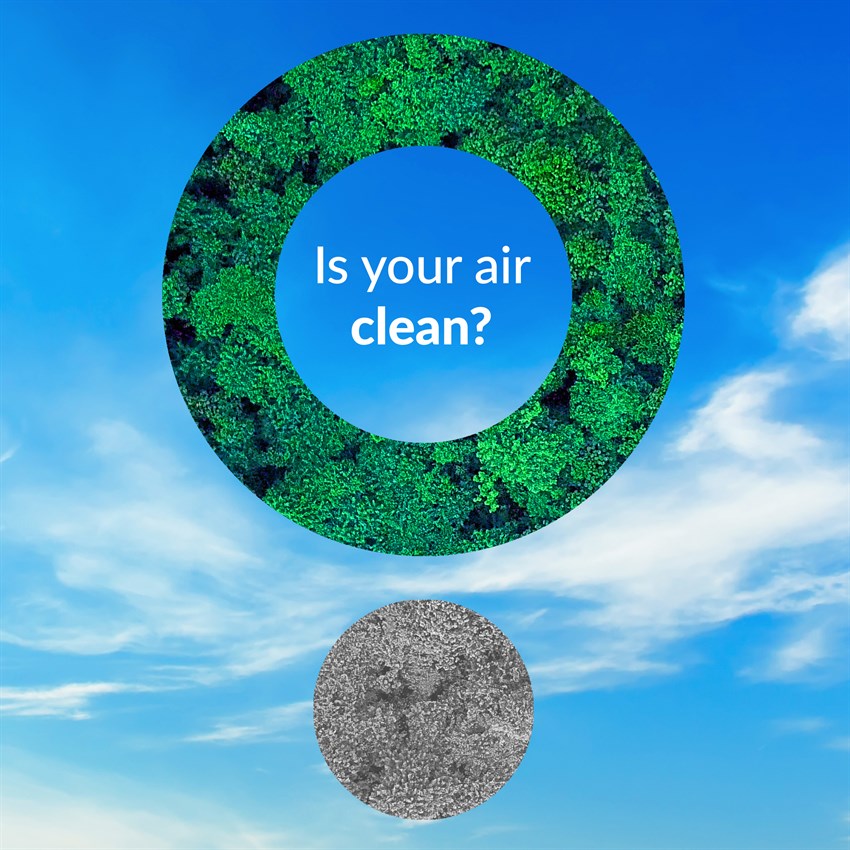
Is your air clean?
Many thanks to our sister company, AEP Compressed Air Technologies Ltd for installing our new clean air technology and delivering leading ISO 8573-1:2010 Class 1.2.1 clean air suitable for critical manufacturing of medical and food components, helping support and enhance our life science and aerospace vertical capabilities.
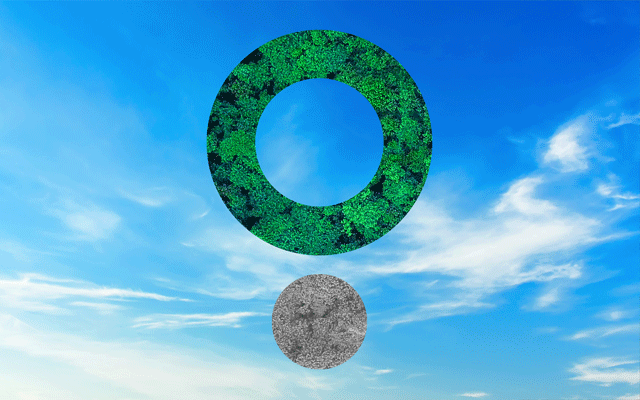
So why do we require clean air?
Hygiene is a critical element of medical equipment and component manufacture. While we typically think of compressed air and the way it delivers reliable power in dirty, grimy conditions, in certain applications there’s a strong connection between compressed air and health, as in life science.
SBR serves the life science industry with a growing number of parts, and demands oil-free compressed air to help keep our products free from contaminants. In order to ensure 100 percent oil-free air, SBR relies on the ISO air purity standards that yield both Class 0 certification and total peace of mind. For SBR’s manufacturing our customers demand, 100 percent oil-free compressed air to ensure that safety is the top priority.
Clean, dry air is essential throughout the manufacturing process. Too much moisture in certain applications can compromise critical parts and components, potentially passing on unnecessary risk to the end users. By employing water separators and coalescing filters, contaminants such as water, dust, oil and other particles are eliminated before the air returns to the cold regenerative absorption dryer. The dryer lowers the dew point to -40 Centigrade; the temperature required to qualify for medical use in accordance with the regulatory standards.
Compressed air might not seem like a matter of life-and-death. However, if life science devices are not properly manufactured or packaged, they could do more harm than good. Clean, reliable air is an essential tool, as used by SBR in the life science industries.
Below is a walk-through of the international standards and what they mean:
Specifying air quality (purity) in accordance with ISO8573-1:2010, the international standard for Compressed Air Quality
ISO8573-1 is the primary document used from the ISO8573 series as it is this document which specifies the amount of contamination allowed in each cubic metre of compressed air.
ISO8573-1 lists the main contaminants as Solid Particulate, Water and Oil. The purity levels for each contaminant are shown separately in tabular form, however for ease of use, this document combines all three contaminants into one easy-to-use table.
Selecting purification equipment to comply with ISO8573-1:2010 air quality standard
Simple guidelines for the selection of purification equipment
1. Purification equipment is installed to provide air quality and you must first of all identify the quality of compressed air required for your system. Each usage point in the system may require a different quality of compressed air dependent upon the application. Using the quality classifications shown in ISO8573-1:2010 will assist your equipment supplier to quickly and easily select the correct purification equipment necessary for each part of the system.
2. ISO8573-1:2010 is the latest edition of the standard. Ensure it is written in full when contacting suppliers. Specifying air quality as ISO8573-1, ISO8573-1:1991 or ISO8573-1:2001 refers to the previous editions of the standard and may result in a different quality of delivered compressed air.
3. Ensure that the equipment under consideration will actually provide delivered air quality in accordance with the quality classifications you have selected from ISO8573-1:2010.
4. When comparing coalescing filters, ensure that they have been tested in accordance with both the ISO8573-2, ISO8573-4 and ISO12500-1 standards.
5. Ask for independent validation of product performance by a third party.
6. For peace of mind, ensure the manufacturer provides a written guarantee of delivered air quality.
7. Oil-free compressor installations require the same filtration considerations as oil lubricated compressor installations.
8. When considering the operational costs of coalescing filters, only compare the initial saturated pressure loss, as dry pressure loss is not representative of performance in a normally wet compressed air system. ISO12500-1 requires pressure losses for coalescing filters to be recorded when the element is saturated.
9. Look at the blockage characteristics of the filter. Just because it has a low starting dp, doesn’t mean it will remain low throughout the filter element’s lifetime. Energy costs should always be calculated based upon the blockage characteristics of the filter, not just initial saturated dp. Ask supplier for verification of blockage characteristics.
10. Look at the total cost of ownership for purification equipment (purchase cost, operational costs and maintenance costs), a low initial purchase price, may look inviting, but may end up costing significantly more in terms of poor air quality and high operational costs.
Specifying air purity in accordance with ISO8573-1:2010
When specifying the purity of air required, the standard must always be referenced, followed by the purity class selected for each contaminant (a different purity class can be selected for each contaminant if required).
An example of how to write an air quality specification is shown below:
ISO 8573-1:2010 Class 1.2.1
ISO 8573-1:2010 refers to the standard document and its revision, the three digits refer to the purity classifications selected for solid particulate, water and total oil. Selecting air purity class 1.2.1 would specify the following air quality when operating at the standard’s reference conditions:
Class 1 Particulate
In each cubic metre of compressed air, the particulate count should not exceed 20,000 particles in the 0.1 - 0.5 micron size range, 400 particles in the 0.5 - 1 micron size range and 10 particles in the 1 - 5 micron size range.
Class 2 Water
A pressure dewpoint (PDP) of -40°C or better is required and no liquid water is allowed.
Class 1 Oil
In each cubic metre of compressed air, no more than 0.01mg of oil is allowed. This is a total level for liquid oil, oil aerosol and oil vapour.
ISO8573-1:2010 Class Zero
• Class 0 does not mean zero contamination
• Class 0 requires the user and the equipment manufacturer to agree contamination levels as part of a written specification
• The agreed contamination levels for a Class 0 specification should be within the measurement capabilities of the test equipment and test methods shown in ISO8573 Pt 2 to Pt 9
• The agreed Class 0 specification must be written on all documentation to be in accordance with the standard
• Stating Class 0 without the agreed specification is meaningless and not in accordance with the standard
• Several compressor manufacturers claim that the delivered air from their oil-free compressors is in compliance with Class 0
• If the compressor was tested in clean room conditions, the contamination detected at the outlet will be minimal. Should the same compressor now be installed in a typical urban environment, the level of contamination will be dependent upon what is drawn into the compressor intake, rendering the Class 0 claim invalid
• A compressor delivering air to Class 0 will still require purification equipment in both the compressor room and at the point of use for the Class 0 purity to be maintained at the application
• Air for critical applications such as breathing, medical, food, etc typically only requires air quality to Class 2.2.1 or Class 2.1.1
• Purification of air to meet a Class 0 specification is only cost effective if carried out at the point of use